A staggering one-fifth of the world’s carbon emissions come from the manufacturing and production sectors. Companies in these sectors not only face growing pressure to decarbonize — they must also adapt to new risks and opportunities arising from a changing climate. But first, they need a solid understanding of where their greenhouse gases are coming from.
In this article, we provide a baseline picture of common emissions sources in manufacturing, based on Persefoni’s analysis of data from the CDP. This emissions profile is meant to serve as a starting point, enabling organizations to zero in on the activities and emissions sources that are likely worth measuring, so they can streamline their carbon accounting.
What is an Emissions Profile?
A snapshot of leading carbon sources.
One of the first steps in developing a decarbonization strategy and preparing for climate disclosure is understanding which greenhouse gas (GHG) sources you need to track to align with global standards and industry best practices. This is where an emissions profile comes in. It provides a snapshot that shows the typical greenhouse gas-producing activities in a given industry.
Organizations can use their sector’s emissions profile to identify the business activities that will likely be material for them. They can then move on to collecting the specific financial and operational data needed for robust, audit-grade carbon accounting — and for making effective reductions.
The Manufacturing Sector Landscape
Supply chain disruptions, regulatory pressure, rising energy costs.
Climate change has given rise to a number of new threats for companies in manufacturing. They face physical risks, like the disruption of supply chains, severe weather, and water shortages. They also face geopolitical risks, like rising energy costs and new climate regulations, including carbon tax policies like the EU’s Carbon Border Adjustment Mechanism (CBAM).
New opportunities are emerging, too. Embracing sustainability (increasing energy efficiency, for example) can not only lead to cost savings but often creates a competitive advantage, especially as more stakeholders and customers demand low-carbon products.
In manufacturing, much of this opportunity lies in embracing the principles of a circular economy — reducing waste and stretching the life cycle of products. “Product design must focus on eliminating waste and emissions,” explains Persefoni Senior Director of Carbon Solutions Jacob Madsen, who has spent the past 20 years helping some of the largest global companies and governments reduce their carbon footprints. “Products and packaging can be circulated by being maintained, reused, repaired, and if that doesn’t work, recycled.”
The Emissions Profile of Manufacturing
A starting point for comprehensive carbon accounting.
Emissions in the manufacturing sector come from a wide range of activities up and down the value chain. Below, we provide a breakdown of top emissions sources reported in subcategories across the sector.
This emissions profile is based on Persefoni’s analysis of carbon benchmarking data from the CDP, an organization that gathers annual voluntary climate reports from companies worldwide. It is intended to provide a roadmap for more comprehensive carbon accounting by helping companies understand the business activities that may make up their carbon footprints.
Our analysis follows the CDP’s classification of manufacturing, which includes subcategories like electrical equipment, transportation equipment, paper products, and plastics. Manufacturing of apparel — a significant driver of emissions — is profiled separately.
Electrical and Electronic Equipment Manufacturing
This large sub-category includes the manufacturing of primary and secondary cell batteries, communications equipment, computer hardware, commercial HVAC appliances, household appliances, semiconductors, silicon, and more. For companies in this category, material emissions include:
Scope 1 Direct Emissions
- Stationary combustion from furnaces, backup generators, and fuel-based manufacturing equipment.
- Mobile combustion from a fleet, if vehicles are owned or leased by the company.
- Fugitive emissions from refrigerants used for air conditioning and cooling equipment in facilities or car repairs.
Scope 2: Indirect emissions
- Purchased electricity used to power offices and facilities.
- Purchased heat and steam used for power, heat, and cooling at manufacturing facilities.
Scope 3: Indirect emissions
- Purchased goods and services, including raw materials as well as goods procured to support daily operations.
- Capital goods, including fixed assets like manufacturing equipment.
- Fuel and energy-related activities that are not captured in scopes 1 and 2. This includes well-to-tank upstream emissions from purchased fuels, generation of purchased electricity, and transmission and distribution losses.
- Waste generated from operations, including waste volumes, transportation, and treatment services.
- Use of sold products, including fuel and energy consumption.
- End-of-life treatment for sold products, including landfilling, incineration, and recycling.
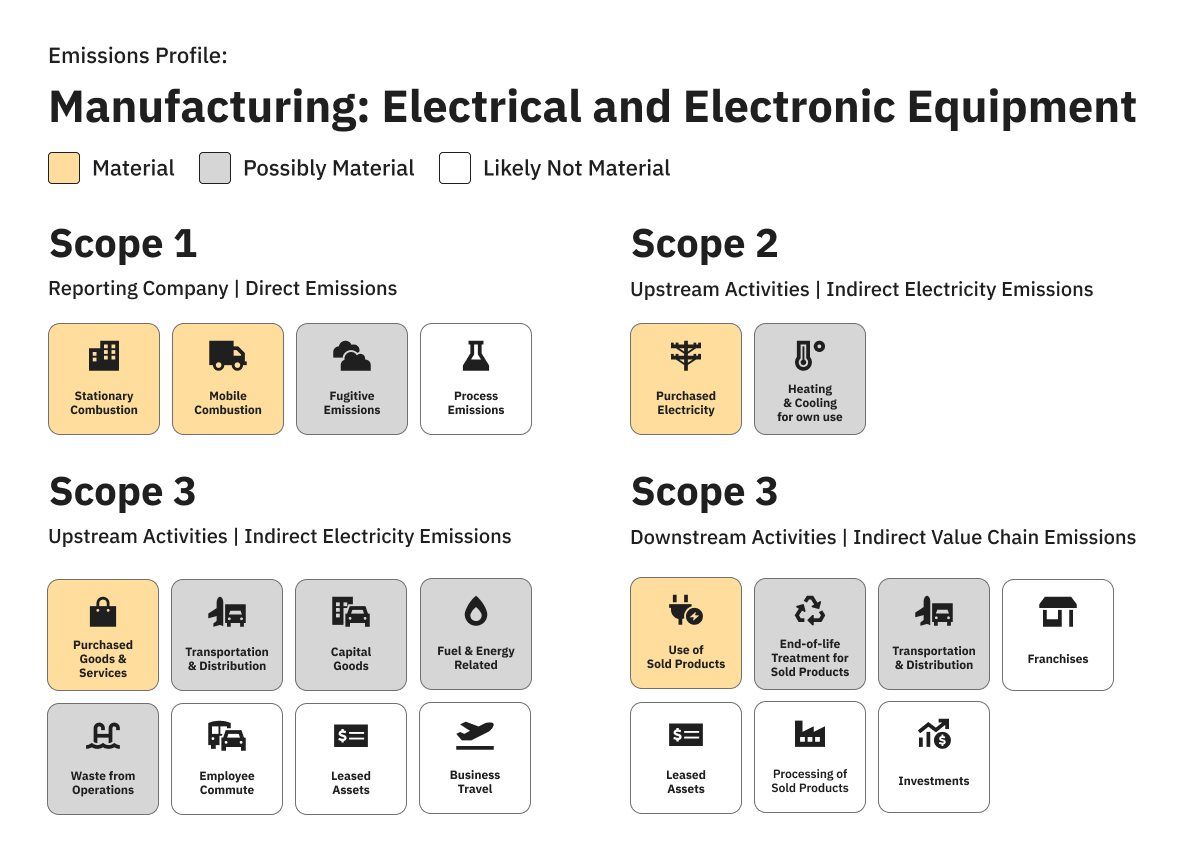
Transportation Equipment Manufacturing
This sub-category includes the manufacturing of automobiles, alternative fuel vehicles, aircraft, missiles, spaceships, trains, ships, recreational vehicles, and more. For companies in transportation equipment manufacturing, material emissions include:
Scope 1 Direct Emissions
- Stationary combustion from furnaces, backup generators, and fuel-based manufacturing equipment.
- Mobile combustion from an owned fleet or forklifts.
- Fugitive emissions from refrigerants used in AC and cooling equipment in facilities and vehicles.
Scope 2 Indirect Emissions
- Purchased electricity used in offices and facilities.
- Purchased heat and steam used for power, cooling, and heat at manufacturing facilities.
Scope 3 Indirect Emissions
- Purchased goods and services, including direct (raw materials used for manufacturing) and indirect (goods procured to support daily company operations).
- Fuel and energy-related activities not included in scopes 1 and 2, including well-to-tank upstream emissions from purchased fuels, generation of purchased electricity, and transmission and distribution losses.
- Waste generated from operations, including waste volumes, transportation, and treatment services.
- Fuel and energy consumption from the use of sold products — a substantial consideration for this industry.
- End-of-life treatment of sold products, including landfilling, incineration, and recycling.
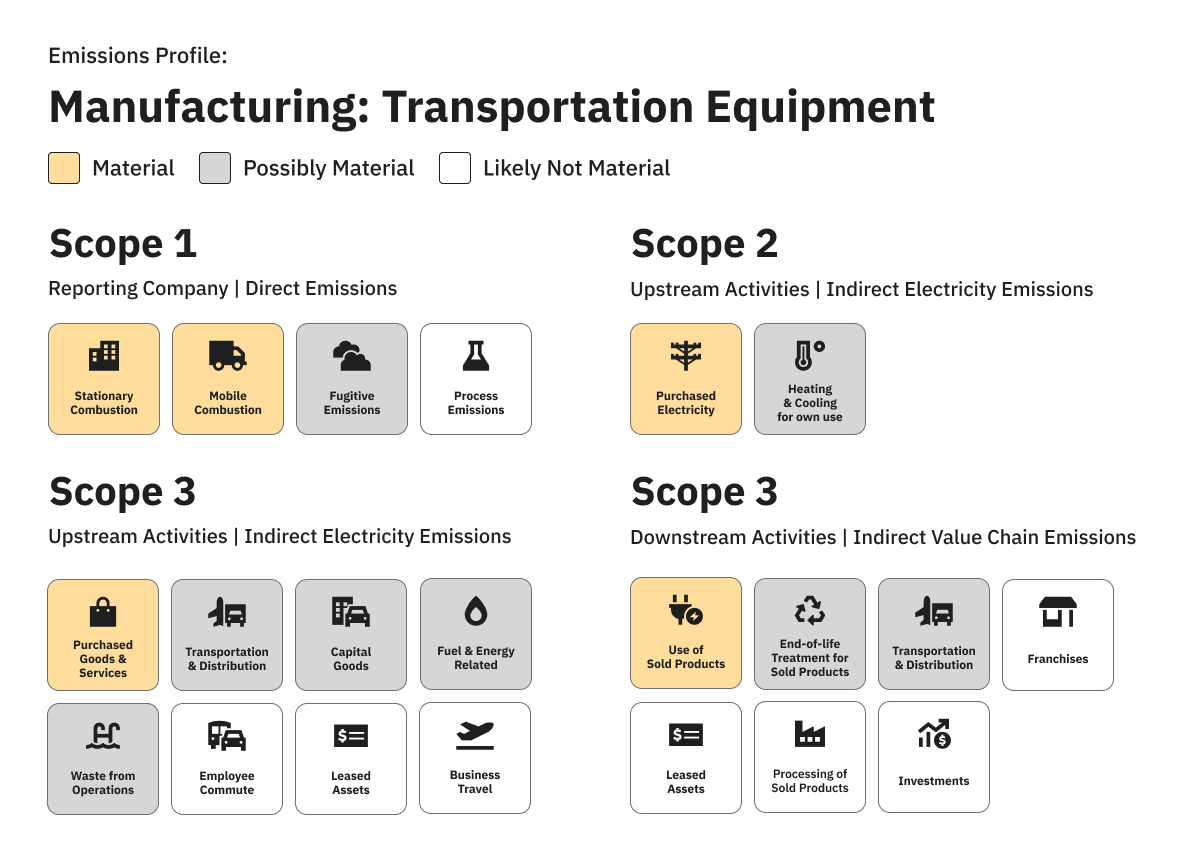
Paper Products and Packaging
This sub-category encompasses the manufacturing of paper-based containers, cardboard packaging, food containers, and paper bags, as well as household products, sanitary products, stationary, and other paper products. For companies in this category, material emissions include:
Scope 1 Direct Emissions
- Stationary combustion from furnaces, backup generators, and fuel-based manufacturing equipment.
- Mobile combustion from an owned fleet or forklifts.
- Fugitive emissions from refrigerants used in AC and cooling equipment in facilities and vehicles.
Scope 2 Indirect Emissions
- Purchased electricity used in offices and facilities.
- Purchased heat and steam used for power, cooling, and heat at manufacturing facilities.
Scope 3 Indirect Emissions
- Purchased goods and services, including direct (raw materials used for manufacturing) and indirect (goods procured to support daily company operations). These can be substantial due to deforestation for paper.
- Capital goods, including fixed assets such as manufacturing equipment.
- Fuel and energy-related activities not included in scopes 1 and 2, including well-to-tank upstream emissions from purchased fuels, generation of purchased electricity, and transmission and distribution losses.
- Transportation distribution from upstream and downstream sources, including purchased third-party transportation and distribution services for inbound, outbound, or inter-company logistics paid for by the reporting company.
- Waste generated from operations, including waste volumes, transportation, and treatment services.
- Processing of sold products, including fuel and energy consumption from manufacturing processes of downstream companies.
- End-of-life treatment of sold products, including landfilling, incineration, and recycling.
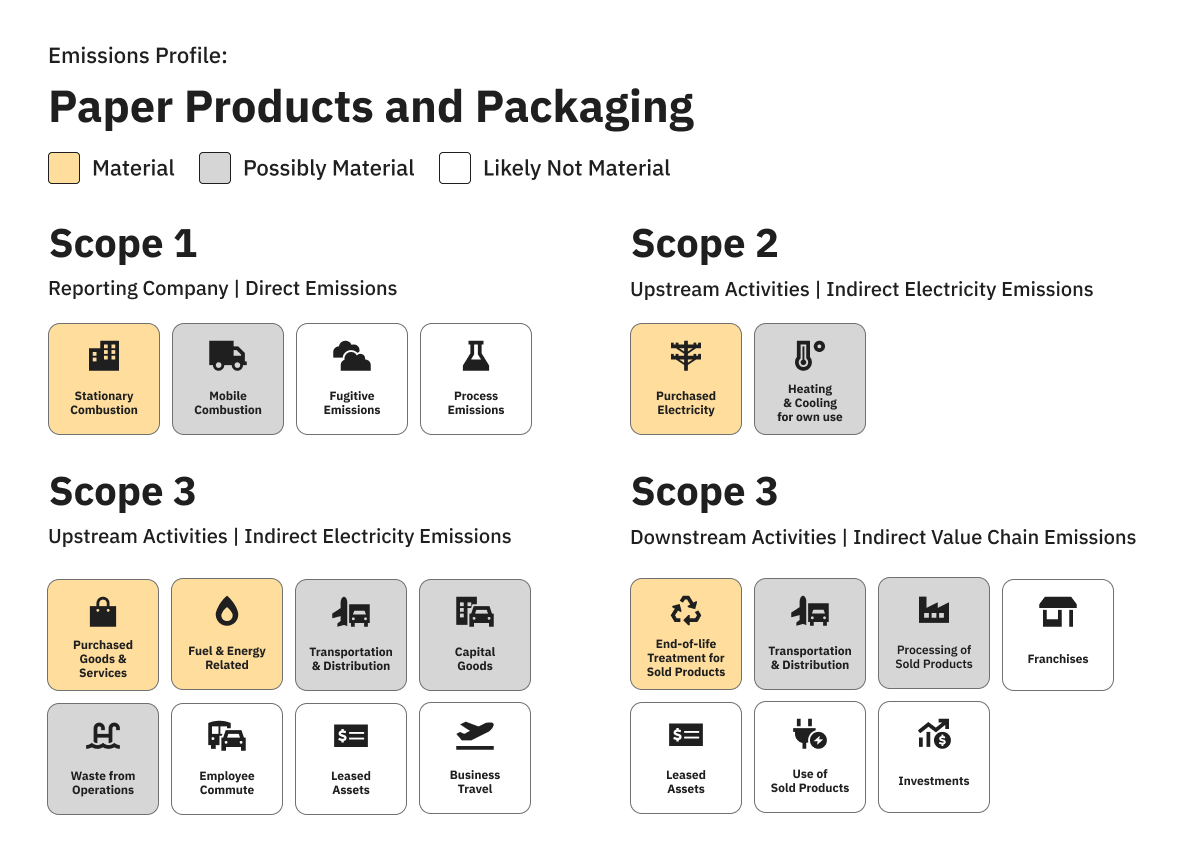
Plastic Products Manufacturing
This sub-category covers the manufacturing of building materials, containers, film and sheet plastic, household plastic products, and packaging materials. For companies in this category, material emissions include:
Scope 1 Direct Emissions
- Stationary combustion from furnaces, backup generators, and fuel-based manufacturing equipment.
- Mobile combustion, likely for transportation from an owned or leased fleet.
- Fugitive emissions from refrigerants used in AC and cooling equipment in facilities and vehicles.
- Process emissions from chemical refineries.
Scope 2 Indirect Emissions
- Purchased electricity used in offices and facilities.
- Purchased heat and steam used for power, cooling, and heat at manufacturing facilities.
Scope 3 Indirect Emissions
- Purchased goods and services, including direct (raw materials used for manufacturing) and indirect (goods procured to support daily company operations). These can be substantial due to deforestation for paper.
- Capital goods, including fixed assets such as manufacturing equipment.
- Fuel and energy-related activities not included in scopes 1 and 2, including well-to-tank upstream emissions from purchased fuels, generation of purchased electricity, and transmission and distribution losses.
- Transportation distribution from upstream and downstream sources, including purchased third-party transportation and distribution services for inbound, outbound, or inter-company logistics paid for by the reporting company.
- Waste generated from operations, including waste volumes, transportation, and treatment services.
- Processing of sold products, including fuel and energy consumption from manufacturing processes of downstream companies.
- End-of-life treatment of sold products — a significant consideration for this industry.
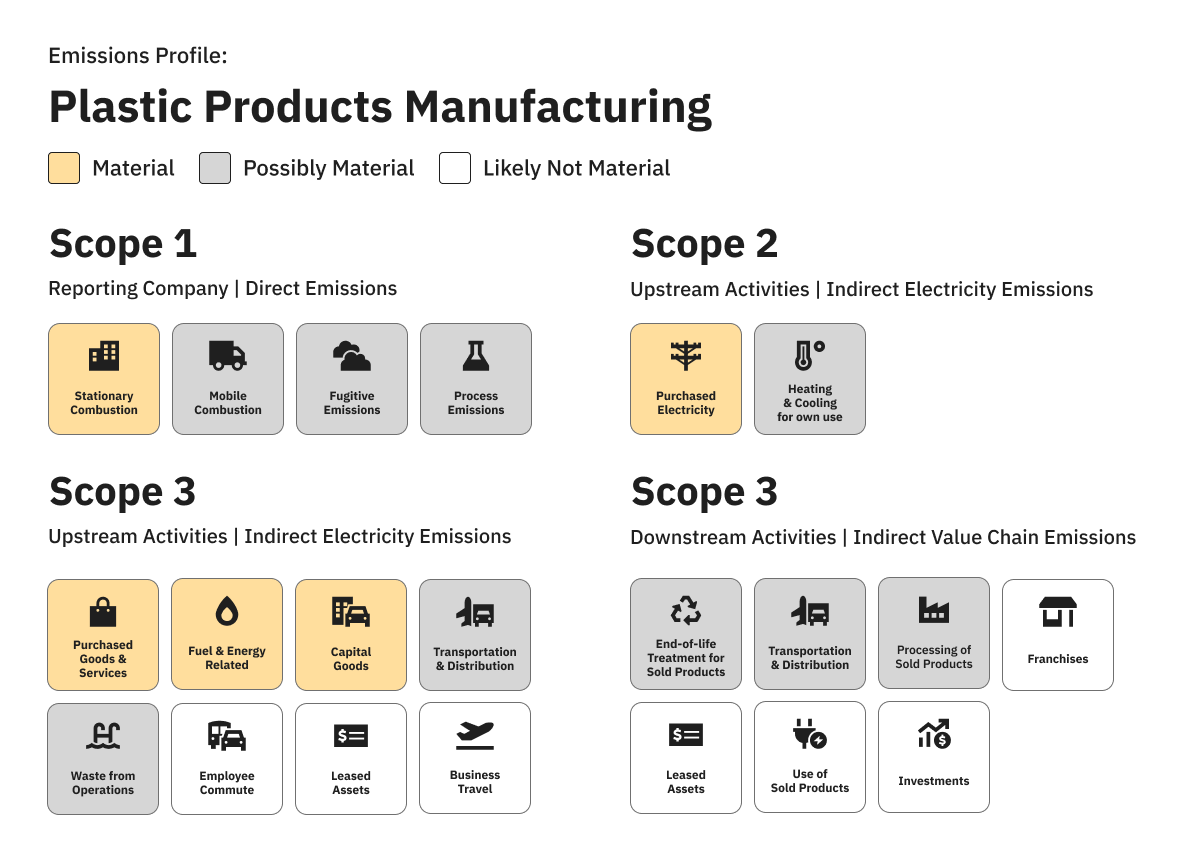
Other Manufacturing
CDP’s sector mapping for manufacturing encompasses a number of other industries with very similar emissions profiles. These include leisure and home products, renewable energy equipment, light manufacturing, and more. Material emissions sources reported by these industries include:
Scope 1 Direct Emissions
- Stationary combustion from furnaces, backup generators, and fuel-based manufacturing equipment.
- Mobile combustion from an owned fleet or forklifts.
- Fugitive emissions from refrigerants used in AC and cooling equipment in facilities and vehicles.
Scope 2 Indirect Emissions
- Purchased electricity used in offices and facilities.
- Purchased heat and steam used for power, cooling, and heat at manufacturing facilities.
Scope 3 Indirect Emissions
- Purchased goods and services, including direct (raw materials used for manufacturing) and indirect (goods procured to support daily company operations). These can be substantial due to deforestation for paper.
- Capital goods, including fixed assets such as manufacturing equipment.
- Fuel and energy-related activities not included in scopes 1 and 2, including well-to-tank upstream emissions from purchased fuels, generation of purchased electricity, and transmission and distribution losses.
- Transportation distribution from upstream and downstream sources, including purchased third-party transportation and distribution services for inbound, outbound, or inter-company logistics paid for by the reporting company.
- Waste generated from operations, including waste volumes, transportation, and treatment services.
- Processing of sold products, including fuel and energy consumption from manufacturing processes of downstream companies.
- Fuel and energy consumption from the use of sold products.
- End-of-life treatment of sold products, including landfilling, incineration, and recycling.
Decarbonization Challenges in the Manufacturing Sector
Supply chain data is crucial.
Raw materials like steel are a top driver of carbon for companies in the manufacturing sector. That means it’s essential to tackle scope 3 supply chain emissions — and they can be extremely difficult to calculate. “It’s hard to trace where materials come from,” Madsen explains. “Often, you’ll just buy steel from several suppliers. You don’t necessarily know how it was produced from mining to production.”
This visibility into the value chain is critical to making informed decisions about how to decarbonize. So is reliable, consistent data. “One of the biggest challenges is getting data that’s good enough to help you implement measures that actually reduce emissions,” Madsen says.
Promising solutions have emerged to address this challenge. For example, an effort is underway to expand access to carbon accounting through free software like Persefoni Pro. Manufacturing companies can share the software with their suppliers at no charge, which allows them to begin collecting more reliable scope 3 data and quickly identify patterns and hot spots. It also lowers the bar for entry into carbon accounting, allowing small suppliers to easily calculate their footprints. “We need to democratize carbon accounting and make it accessible to everyone,” Madsen says. “Once we do that, we can create good, actionable sector data.”
What’s Next? A Playbook for Calculating Emissions in Manufacturing
A step-by-step approach to assessing your footprint.
Many manufacturing companies are just starting out on their decarbonization journeys, and calculating emissions can feel overwhelming. It’s helpful to take a crawl-walk-run approach, with the understanding that your data will likely become more comprehensive and granular over time. Below, we outline key steps to consider as you begin.
1. Create a Project Management Plan
- Secure buy-in: Engaging senior leadership will be crucial for resource allocation and the success of your carbon accounting efforts, especially in the face of budget constraints. Clearly outlining climate risks and opportunities can help cultivate buy-in throughout the organization.
- Designate a project leader: Appoint a dedicated individual to lead your carbon inventory project. This person should have the authority, knowledge, and resources to drive the effort effectively. For many manufacturing companies, the finance function will take the lead.
- Set internal deadlines: Establish clear timelines for each phase of the project. It will help maintain momentum and accountability and ensure you’re prepared to respond to any climate disclosure regulations.
- Develop an IMP: An Inventory Management Plan (IMP) outlines the procedures and methodologies you’ll use for data collection, calculation, and reporting. The plan should be regularly updated to reflect any changes in operations or reporting standards and regulations.
- Ensure consistency: Your IMP should establish repeatable processes for each reporting period. Using automated carbon accounting software is the best way to ensure consistency and transparency year after year.
2. Identify and Assess Emission Sources
- Review potential sources: Consider all possible emission sources as outlined by the GHG Protocol, including scopes 1, 2, and 3. The emissions profile detailed above can serve as a starting point for identifying sources that are likely relevant for your company.
- Assess materiality: Materiality thresholds will vary for each company. You’ll need to conduct a thorough assessment based on your unique operations, industry, and regulatory jurisdiction.
- Create a checklist: Develop a Footprint Source Checklist that details the material sources you’ve identified for tracking and data collection.
3. Gather Emissions Data
- Assign data owners: Identify individuals responsible for collecting data for each emission source. These could be department heads, facility managers, or others.
- Set deadlines: Ensure timely collection of data by establishing and communicating reasonable and clear deadlines.
- Collect data: Scope 1 and 2 data are typically straightforward to collect, as they rely on internal energy consumption information, while scope 3 is more complex. It will likely call for engagement with suppliers and consideration of end-of-life treatment for the products you manufacture. You can start by identifying your top suppliers and your most carbon-intensive materials.
- Conduct quality assurance: Designate a person or team to review the data you collect for accuracy and completeness. This will save time later on, especially if you are required to meet climate disclosure regulations.
4. Engage Suppliers Directly
- Streamline communication: You’ll need to work closely with your suppliers to gather detailed data, understand their processes, and ultimately set expectations for future improvements. Using integrated carbon accounting software can greatly facilitate communication and improve data quality.
- Incentivize emissions reductions: Once you’ve collected data, you can begin to source preferentially from lower-emission companies and encourage suppliers to adopt practices that reduce their carbon footprints.
Looking Ahead
The world cannot decarbonize effectively without the participation of the manufacturing sector — and more stakeholders and regulators are beginning to recognize that. For companies in this sector, addressing emissions from raw materials and the lifecycle of products will be crucial. This is where carbon accounting software comes in. It facilitates communication with suppliers and streamlines the identification of emissions hot spots — ultimately leading to more efficient and effective reductions. As access to carbon accounting software increases, data for the sector will improve, which benefits everyone.
“If everyone uses Persefoni Pro year after year, we can start to build granular databases and begin to see sector/industry emission patterns, and companies will be able to make more informed decisions on where the most decarbonization potential lies.” - Jacob Madsen, Senior Director of Carbon Solutions at Persefoni